Most Manufacturers of more than one product can define some difference between the products they produce. Sometimes, those differences affect how and when those products can be manufactured. These differences in the products can be defined as attributes, which are valuable in building an efficient and executable production schedule.
Many ERP systems are not capable of scheduling the sequence of jobs based on the attributes of the product being produced. Without significant human intervention, tribal knowledge, and daily juggling of orders this can lead to errors on the production schedule which in turn can cause excess waste in manufacturing. This excess waste can be in the form of lost time due to extra changeovers or cleanouts and even damaged products.
PlanetTogether understands that these attributes are critical to scheduling success and has developed Advanced Planning and Scheduling software where Operation Attributes, or characteristics of the job activity that affect cycle times, setup times, yeilds, resource requirements, and cleanouts are utilized to sequence jobs in such a way to reduce waste.
In PlanetTogether, you can define the attribute and define the characteristics of that attribute. This is a unique feature that isn’t a one size fits all approach. Attributes can be defined as colors, flavors, sizes, brands, material types, or anything else unique to your manufacturing plant that affects the schedule. You define what they are, then tell PlanetTogether how much time is needed for setup and how much it costs if the jobs are sequenced together. By defining this setup time and costs, you are giving PlanetTogether the data it needs to sequence jobs to reduce setup time, provide the least cost scenario, utilize capacity to the fullest while honoroing customer order due dates. You also have the option to tell PlanetTogether that two products can never run consecutively. Can your ERP do that?
PlanetTogether also works with Attribute Matrixes that define setup times and costs for each possible sequence combinations in your schedule. Here is an example of a matrix:
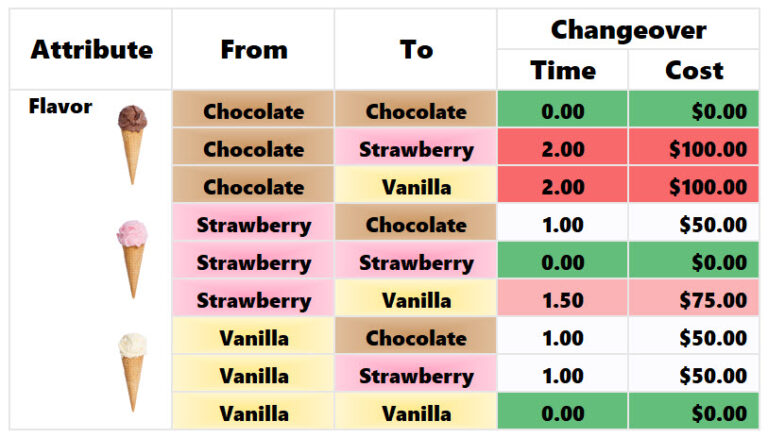
A matrix is very specific, and can be quite complex depending on the number of products and attributes defined. PlanetTogether uses the setup times and costs defined in the matrix to determine the best sequence of jobs depending on the attribute defined. Based on the matrix above, jobs should be sequenced like this to reduce changeover times and costs: 1) Vanilla, 2) Strawberry, and 3) Chocolate. This combination results in 2 hours total setup with a cost of $100. If Chocolate was first, then Vanilla second and Strawberry third the cost would be 3 hours of setup and $150.
To find out more how PlanetTogether and Attributes can help your manufacturing schedule sequencing, please contact Scheduling Solutions today!
CONTACT US
Head Office – 5454 Lena Road, Suite 105 Bradenton, FL 34211, USA
Phone: 941-259-4434
Email: info@schedulingsolutions.net
Website: https://schedulingsolutions.net/
ABOUT US
Scheduling Solutions is uniquely positioned to bring you the finest APS technology with the most experienced APS implementation team in North America.
Most manufacturers recognize that, in order to compete in today’s fast-changing world, they need an APS solution that addresses their unique needs. They also recognize that most APS solutions on the market do not work, cannot work, and will never work.
APS is all we do, and our team can proudly claim that we have implemented successful APS solutions in over 150 manufacturing sites in North America.