
One feature that makes PlanetTogether unique from other APS solutions is the ability to run MRP. Even if you’re ERP runs MRP there may be benefits to using PlanetTogether’s MRP in addition to your current ERP’s MRP.
The key differentiator between your ERP’s MRP and PlanetTogether’s MRP process is that PlanetTogether applies capacity constraints to determine job scheduled dates. An ERP systems MRP will calculate material requirements and job need dates based on an infinite capacity model. Meaning that it assumes that you have an unlimited capacity to manufacture jobs. Let’s repeat that: in your ERP when it calculates the required jobs to meet demand, it assumes your resources have enough capacity to meet ALL required demand at the required dates.
Think about the potential consequences. The primary concern is the timing of when to purchase raw materials. If you run a business that requires materials with a very short shelf life, you want your raw materials to deliver frequently and just in time to meet manufacturing demand. If the ERP’s MRP suggested purchase orders are not constrained by your manufacturing capacity, then you could be bringing in materials too early. This is costly and potentially wasteful.
Now let’s consider how PlanetTogether’s MRP is different. First, PlanetTogether looks at all demand, including sales and forecasts. Then it applies inventory and firmed manufacturing jobs against that demand. If there is not enough inventory or firmed production, then new jobs are created. These jobs are created with a requested date that supports the demand required date. Next, PlanetTogether schedules these new jobs based on your machine capacities and other constraints you may have on your schedule. Each job now has a required date to meet customer demand and a scheduled date, which is the best possible date the product can be produced based on capacity and other constraints built into your schedule. PlanetTogether’s MRP created manufacturing jobs can then be imported into your ERP system using your ERP’s data import processes. MRP can be performed in your ERP against the PlanetTogether jobs to create suggested purchase orders. If you use the scheduled date instead of the required date on the jobs, then your purchase order required dates will be closer to the planned manufacturing schedule. This allows you to keep purchasing costs down by not holding more raw materials than you need to support manufacturing’s capability to execute the demand.
ABOUT US
Scheduling Solutions is uniquely positioned to bring you the finest APS technology with the most experienced APS implementation team in North America.
Most manufacturers recognize that, in order to compete in today’s fast changing world, they need an APS solution that addresses their unique needs. They also recognize that most APS solutions on the market do not work, cannot work, and will never work.
APS is all we do, and our team can proudly claim that we have implemented successful APS solutions in over 150 manufacturing sites in North America.
CONTACT US
Head Office – 5454 Lena Road, Suite 105 Bradenton, FL 34211, USA
Phone: 941-259-4434
Email: info@schedulingsolutions.net
Website: https://schedulingsolutions.net/
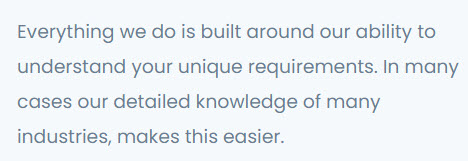